李林
(广州钢铁股份有限公司,广东广州 510381)
摘 要:详细分析了精轧机机架轴承平衡油缸漏油的三种情况及其产生的原因,指出了这种油缸结构上存在的缺陷,提出了相应的改进措施。
关键词:精轧机;轴承平衡油缸;漏油
1 前言
广州钢铁股份有限公司炼钢总厂棒材生产线是引进意大利达涅利公司的全连续棒材轧制生产线。该生产线的6台精轧机组使用达涅利公司较早开发的无牌坊短应力轧机,通过液压马达调节辊缝。辊缝调节时,液压马达转动,带动蜗杆轴,把动力同时传递到四个涡轮、四条拉杆,拉杆转动使轴承座对称同步移动而起调节轧辊中心距的作用。拉杆和轴承座安装在轧机立柱上,8个平衡油缸安装在立柱内,通过柱塞的推力支撑轧辊轴承座,使上下轴承座预张紧,类似弹簧作用,平衡油缸在生产过程中长期保压,以保证辊缝的稳定。平衡油缸中任何一个油缸泄漏,均可引起辊缝变化失稳而导致次品或堆钢事故。
2 存在问题
投产初期,由于产量比较低,精轧机机架运行比较稳定,但随着产量的提高、品种规格的增加和使用年限长,设备磨损加剧,在生产中经常发现精轧液压站油位非正常下降的故障,经检查,发现大都由于轴承平衡油缸漏油所致。平衡缸漏油既增加液压油的消耗,又污染环境,而且由于泄漏引起的辊缝变化,易造成堆钢或产生次品,严重时可导致崩孔和轧辊断裂事故。由于柱塞安装在立柱内,若出现漏油处理比较困难,须卸下轧机,离线拆卸机架,装辊也要投入大量人力和时间,对生产组织和工艺准备产生非常不利的影响。
3 原因分析
精轧机机架轴承平衡油缸结构见图1,其柱塞头密封使用唇形密封圈,柱塞杆密封使用O形圈和P6单唇防尘圈。根据设计要求的动作原理,柱塞头密封起主要密封作用,柱塞杆密封和防尘圈主要作用是防止外面的脏物进入平衡缸油腔内。正常情况下,如柱塞头密封可靠,有杆腔不应该有油,柱塞杆靠机架自重缩回。平衡油缸漏油,主要有以下几种情况。
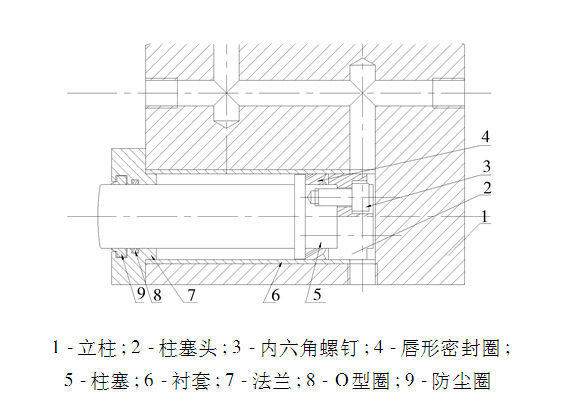
图1 精轧机机架轴承平衡油缸结构图
(1)使用进口的机架和柱塞、柱塞头,当更换唇形密封圈后,在机械手装置上试压就开始漏油。
唇形密封圈是一种具有自封作用的密封圈,它依靠唇部紧贴密封偶合件表面,阻塞泄漏通道而获得密封效果(其密封机理见图2)。无内压时,仅仅因唇尖变形而产生很小的接触压力,在密封的情况下,与密封介质接触的每一点上均有与介质压力相等的法向压力,所以唇形圈底部将受到轴向压缩,唇部受到周向压缩,与密封面接触变宽,同时接触应力增大。当内压升高时,接触压力的分布形式和大小进一步改变,唇部与密封面配合更紧密,密封性能更好。在这里,柱塞密封使用不等高唇密封,长唇紧贴密封沟槽(这里指柱塞杆)底部,与非运动表面接触;短唇与运动表面接触,降低动作摩擦力。拆卸检查发现使用了杆用的Yx圈,机械手装置压力较低,主要靠长唇产生的预压力密封,短唇与活塞杆非运动表面接触,过盈量产生的预压力不足,与缸底接触压力过小而起不了密封作用。

图2 阻塞泄漏通道的密封机理图
(2)使用进口的机架,当更换国产的柱塞、柱塞头后出现漏油。一般地,国产的柱塞和柱塞头备件是通过对进口机架的柱塞和柱塞头进行测绘,然后根据其尺寸制造的。由于机架使用年限长,柱塞、柱塞头都存在不同程度的变形、磨损,需及时更换,以保证生产。使用进口的机架,更换国产柱塞、柱塞头备件后,在机械手装置上试压,没有出现漏油,但投入使用就开始漏油。Z初估计是因密封件老化而引起的,但更换新的密封件后仍然漏油。Z后检查柱塞和柱塞头,重新测量,发现国产的柱塞头(见图3a)沟槽尺寸和原装进口的柱塞头对比大了1mm。本应为4mm,现在是5mm。这可能是测绘时出现偏差造成的。沟槽过深,导致和柱塞杆及活塞用唇形密封件装配后,柱塞头紧紧压死密封件外唇边,液压油不能进入张开的唇口内。压力低时,靠唇边变形产生的预压力还可密封,当压力升高到一定程度时,由于液压油不能到达唇口内,产生不了流体压力,而密封件内唇的预压力不足于密封高压油,从而引起泄漏。机械手装置液压系统压力约7MPa,生产线压力一般超过10MPa,因而试压不漏油而投入使用漏油。把活塞R0.3的圆角(见图3a)改为2×45°的倒角(见图3b)后,使压力油可进入唇口,唇边在压力下张开贴紧缸体内壁密封,从而解决了漏油问题。
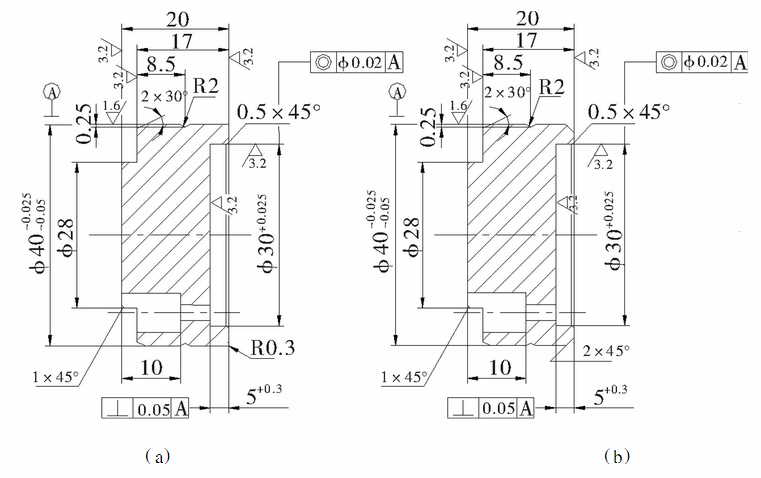
图3 柱塞头尺寸
(3)使用进口的机架和柱塞、柱塞头,当更换国产Yx密封圈后,在机械手装置上试压不漏油,投入生产线使用出现漏油。
上述漏油情况发生后,我们拆下来检查发现国产的Yx密封圈唇高为11mm,而标准为10mm,导致装配后柱塞头压死外唇,压力油不能进入密封唇口内,单纯靠内唇预压力密封,压力超过预压力时就出现漏油。换为标准的活塞用Yx密封圈后,消除故障。
另外,轧钢线环境比较恶劣,分析平衡油缸结构和密封形式,发现还存在另外可引起泄漏的缺陷:①由于轧机使用环境恶劣,多粉尘和污水,还有辐射高温,防尘圈若为采用丁腈橡胶的P6型防尘圈,氧化铁皮容易刮伤唇口,不能有效防治污染物进入柱塞缸内。②柱塞杆密封使用O形圈,摩擦阻力大,容易发生扭曲和挤出而失效。③衬套壁厚太小(只有2mm),装入立柱容易变形,造成缸筒同心度和圆度偏差太大,影响密封件的密封效果。而且衬套和立柱焊接时也容易产生焊接变形。④法兰和缸筒没有密封。虽然有杆腔不应该有油,但当活塞密封失效时,液压油跑到有杆腔而有可能从法兰密封面泄漏。
4 改进措施
由以上分析可知,只要对平衡油缸的密封结构和装配尺寸稍作改进,就可解决漏油问题。
(1)将P6型防尘圈改为P8型,此种密封带双唇口,对脏物的刮擦能力强、耐磨损,可有效刮掉柱塞杆上的氧化铁皮等杂物,保持柱塞杆和杆密封,防止污物进入液压系统中。
(2)法兰增加一沟槽,安装O形密封圈,装配后O形圈和衬套(缸筒)内壁接触而起密封作用。
(3)柱塞与柱塞头配合槽深改为4mm,外圆倒较大的角度,装上Yx密封圈后,Yx密封圈和活塞轴向有1mm间隙,以保证压力油可以到达唇口。
(4)正确选用活塞用唇形密封圈,在这里选用MERKEL公司的NA300型U型密封圈,尺寸为30mm×40mm×10mm,无论是原装进口还是国产的柱塞、柱塞头备件均可使用。
(5)国产的柱塞头因沟槽尺寸比较深,互换性较差,所以必须上车床车去1mm,外圆倒角2×45°,这样才可使用在原装的柱塞上。
(6)国产化精轧机机架制造时,要求衬套加厚(见图4),立柱原来的内孔由44mm加大至50mm,以和衬套过盈配合装配,然后焊接,表面磨平。
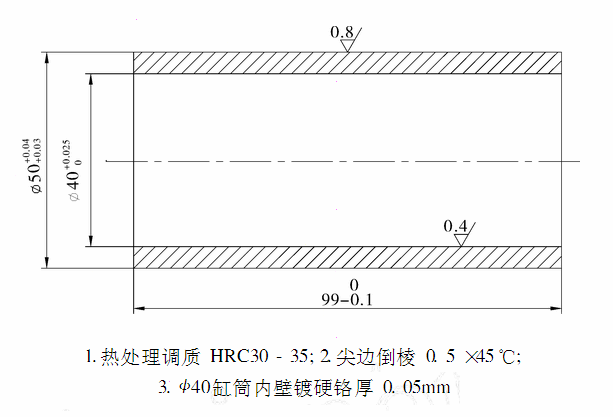
图4 改造后衬套的尺寸
5 效果分析
通过以上改进,漏油问题彻底解决。大幅提高了密封件的密封性能和使用寿命,较改进前寿命提高3倍以上。改进前密封件Z多可使用3个月,改进后正常使用寿命1年以上。大幅降低了液压油的消耗,改进前精轧液压站每个月添加20桶;改进后每个月添加不不超过8桶,平均每年可节省液压油96桶,直接降低生产成本15万元。减轻了精轧机机架维修和维护劳动强度,平衡油缸漏油检修机架须整体拆卸,耗时费力,平衡油缸漏油处理投入人力3~4人,检修时间需3天;改进后平衡油缸几乎不漏油,机架漏油检修很少,平时只需作日常性维护。提高了设备的综合利用效率和设备承载能力,改进前精轧机机架平衡油缸漏油事故3次/月,每次更换机架需时45min;改进后基本不出现漏油,增加生产时间135min。相应产量增加按120t/h计算约270t,每月增加利润约2.7万元,每年增加约30万。若轴承平衡失稳还引起堆钢和次品事故,则无形中增加生产成本和减少生产作业时间,改进后大大提高了生产的通畅性。另外平衡油缸漏油事故的减少还改善了作业环境和开路冷却水水质,减轻了环境污染和开路循环水外排引起的污染事故。平衡油缸漏油的解决不仅具有显著的经济效益,而且具有节约资源和环保等社会效益。
6 结束语
作为精轧机机架的核心部件,平衡油缸泄漏将对生产造成重大影响。我们根据密封原理,总结多次设备维修和事故处理经验,提出了消除漏油的改进措施,并在实践中反复检验,收到了良好的效果。这对进口设备的国产化和维护维修、备件的国产化、密封结构形式的设计和选型有重要借鉴意义,同时也为国内大量同类型设备的技术改造提供了参考性建议。
参考文献
[1]徐灏.密封[M].北京:冶金工业出版社,1999.
[2]黄迷梅.液压气动密封与泄漏防治[M].北京:机械工业出版社,2004.
来源:《冶金丛刊》2008年4期